VAM® Field Service: Expertise and Innovation Provide High Added Value to Operators During Well Construction
Oil and gas operators have long reaped the benefits of using the VAM® Field Service (VFS) worldwide network of experts to ensure that VAM® best practices are deployed and operations run smoothly for increased integrity and efficiency. Now, leveraging its expertise, VAM® Field Service wish to provide even greater value to their customers through digital and innovative solutions.
A network of skilled technicians
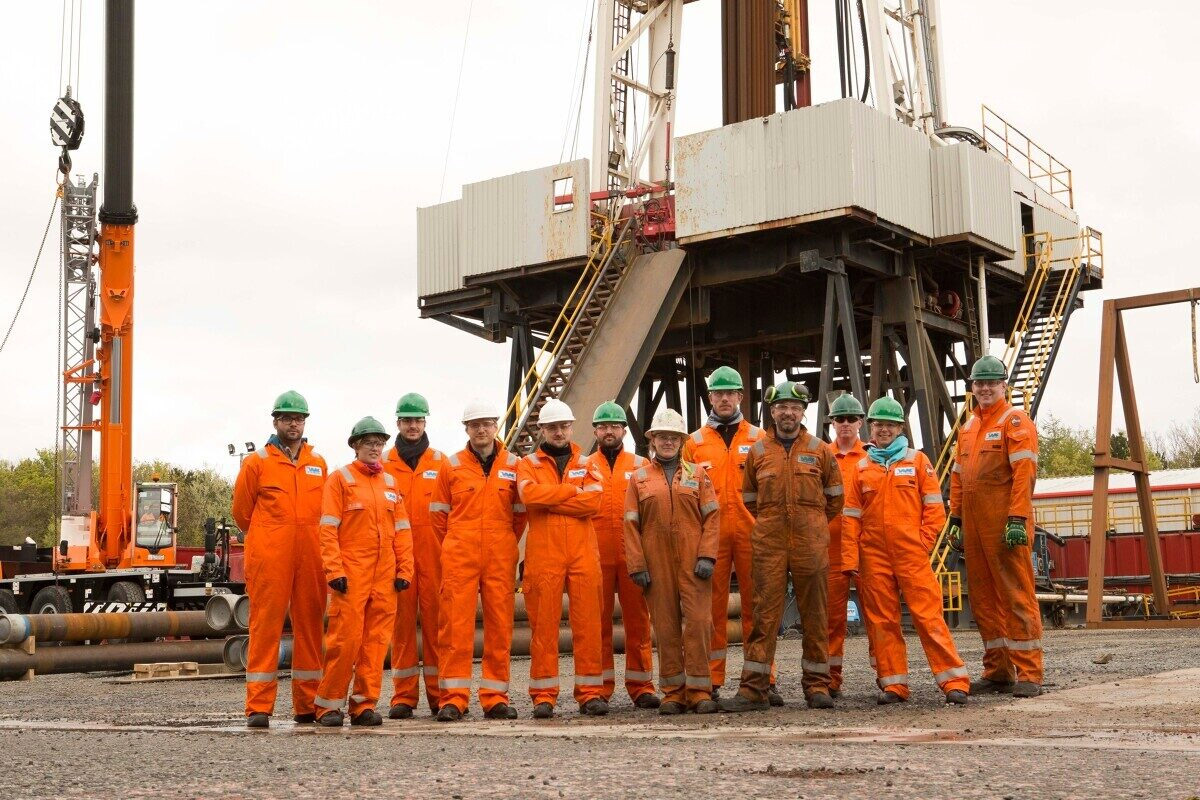
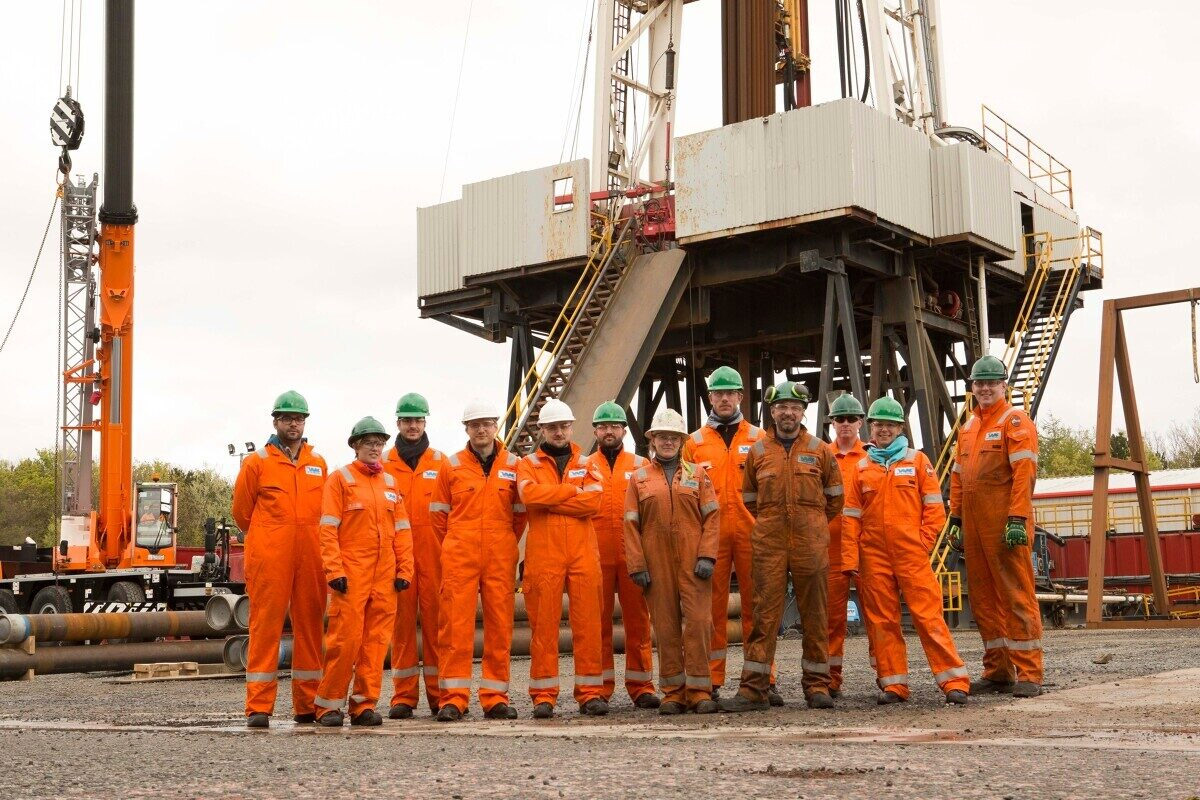
The VAM® Field Service network consists of more than 180 skilled technicians situated in 19 service centers worldwide. These technicians undergo a comprehensive induction training program at the VAM® Academy, which spans a minimum of 10 weeks. Following their training, they receive on-the-job supervision and undergo a Competency Assessment conducted by an assessor certified by OPITO. If the Trainee is approved by an OPITO certified approver, they are awarded a VAM® Field Service Certificate of Approval and officially become a VFS Technician.
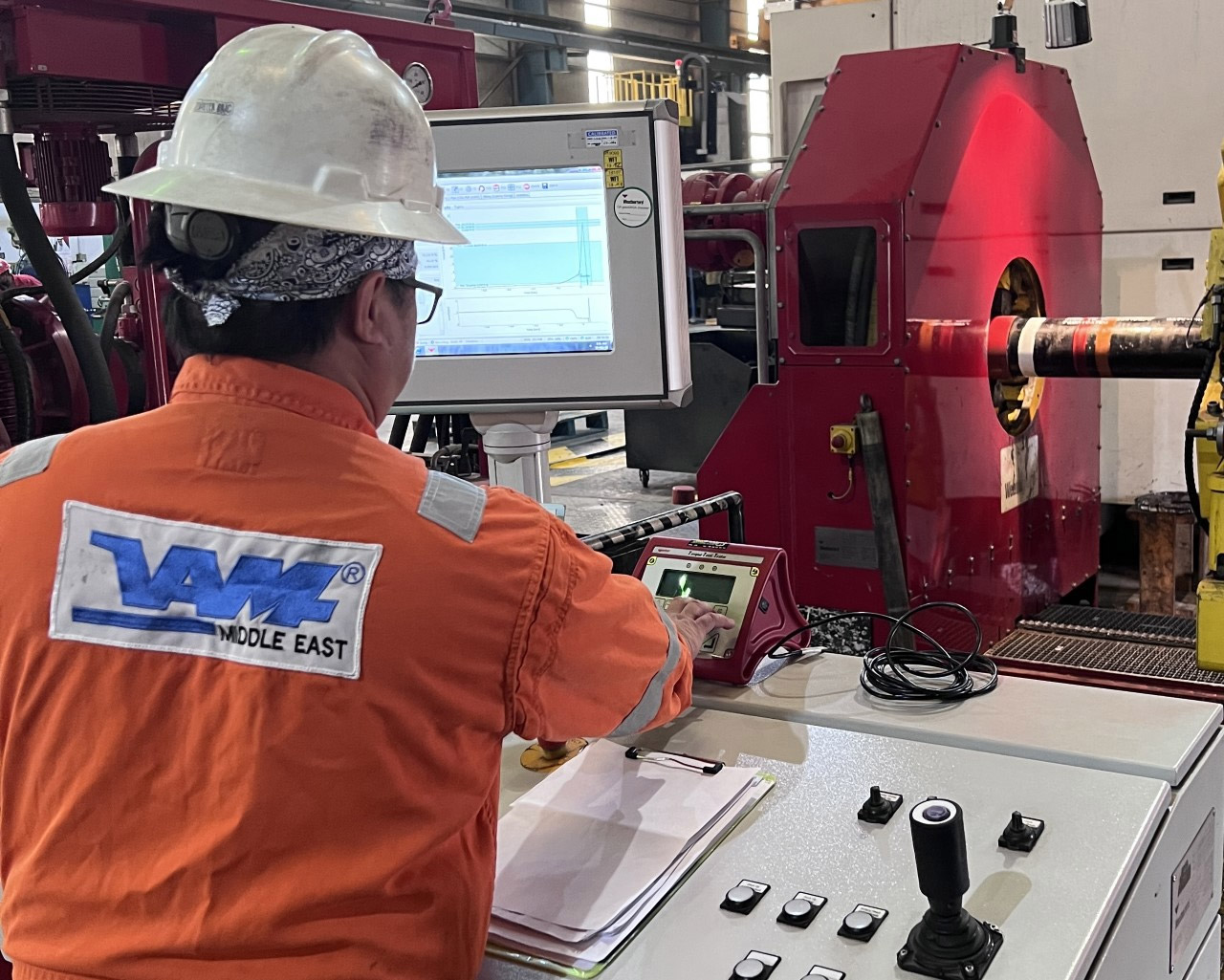
VAM® Field Service’s primary objective is to ensure the correct running of VAM® products. To accomplish this, VFS offers an extensive range of services from the mill to the well. VFS takes pride in assisting its customers by ensuring well integrity, improving safety and rig operating efficiency and reducing costs. Furthermore, our VFS offerings include an array of string integrity management services, which encompass crucial aspects such as, quality and conformity inspections, advisory services, and tool rentals. More recently, VFS in the US can apply Torque Turn Monitoring to running operations using a sensory equipment to graph the connection make-up in the torque vs. turn formatted chart. If the chart shows an abnormality VFS can quickly identify a bad make-up and rectify it.
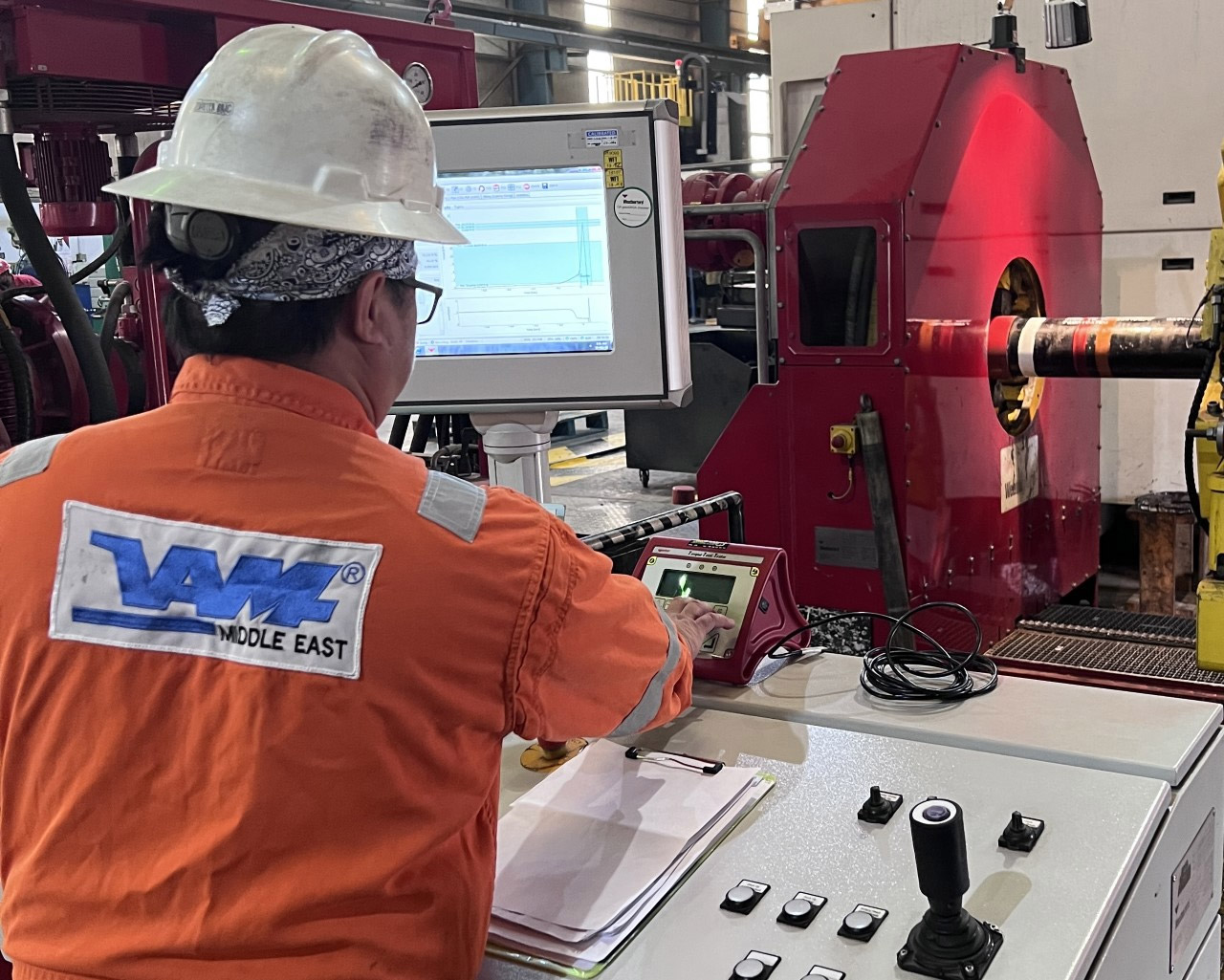
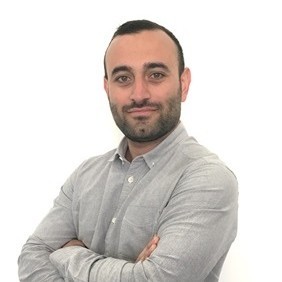
We offer vital support to customers for planning and installation. For instance, based on statistics and our extensive experience, we can provide improved contingency percentages. Additionally, we can offer valuable insights on various aspects, including when inspections are necessary, what the inspection process should be, the duration, and associated costs”
The range of services provided by VAM® Field Service offers numerous advantages that are well recognized and valued by customers. Rig operators can experience improved operational efficiency, reduced risk, and achieve 100% product integrity.
“VFS helps prevent significant issues during running operations”, explains Daniel. “As an example, during a run-in-hole (RIH) completion, a VAM® Tech noticed that the slip type elevator being used was not securely gripping the pipe body but resting on the coupling face of the special bevel which is not designed to lift or carry load. They immediately stopped the operation to rectify the issue before proceeding with the RIH, therefore safeguarding the operation’s safety and integrity”.
Innovating for the future
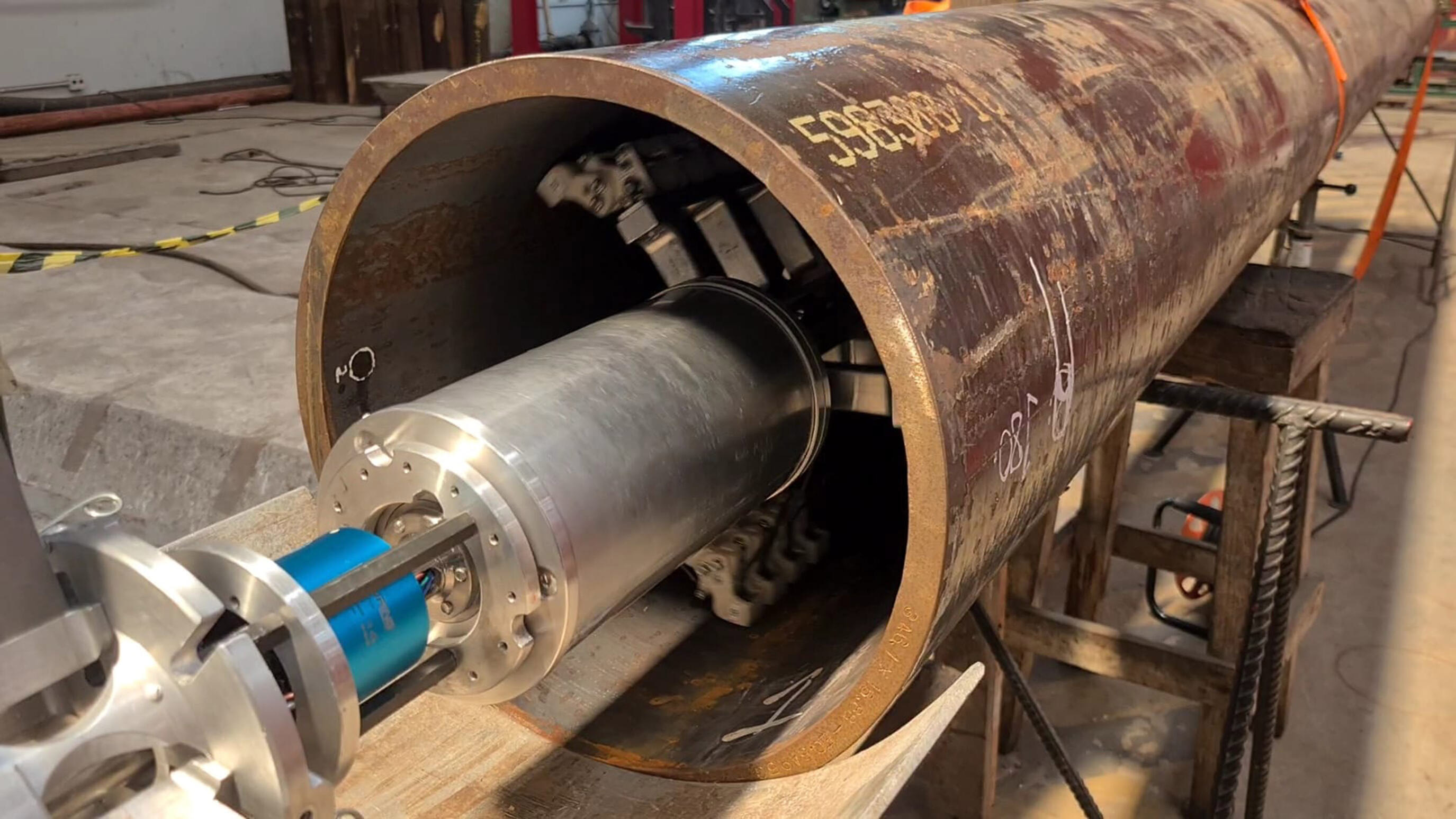
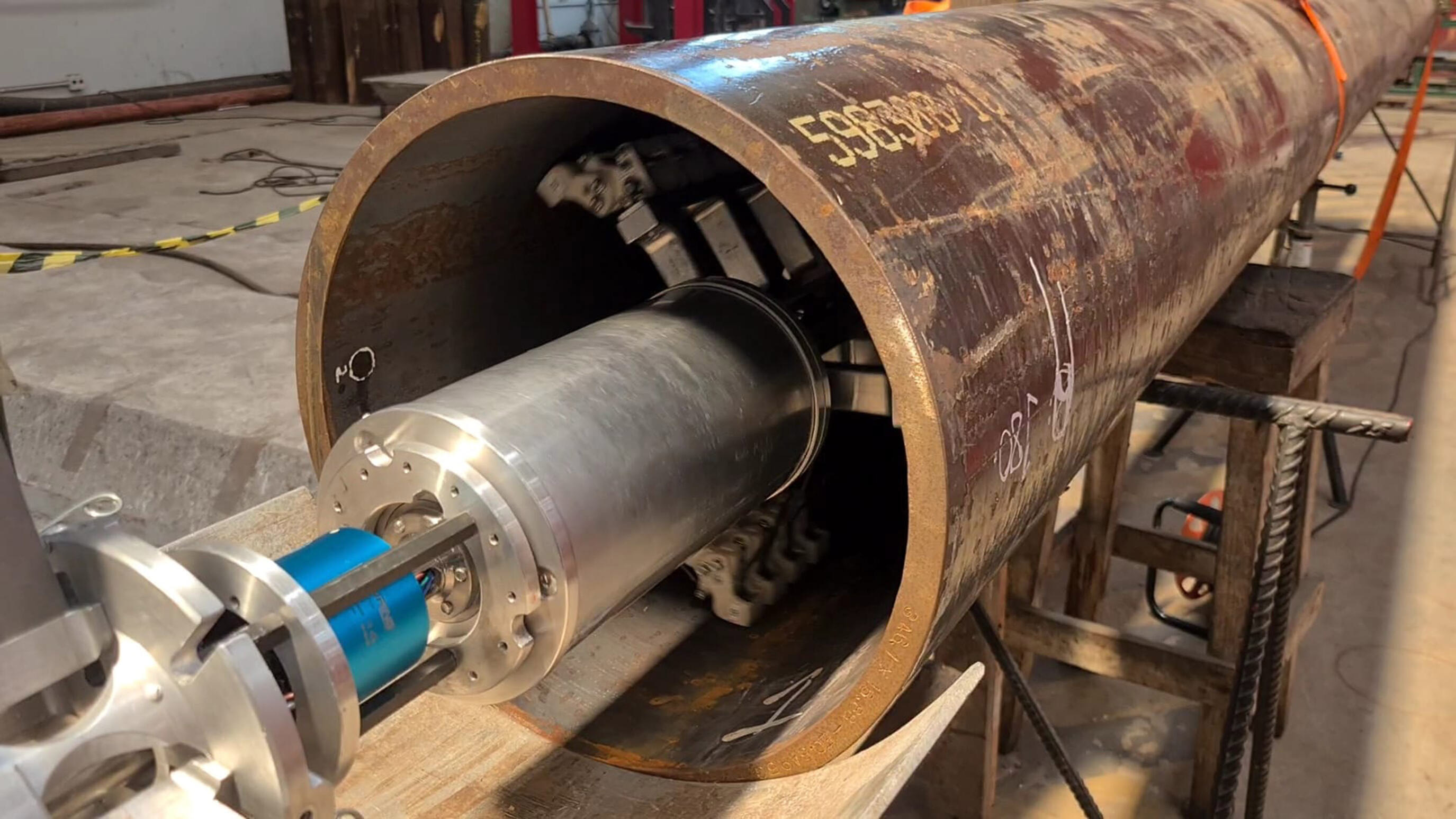
Driven by the willingness to provide customers with even more value through their expertise, VFS continuously seeks opportunities to utilize digital technologies and innovations in order to enhance its offerings. As part of this effort, VFS can perform the Prime Mapping service, which delivers precise casing and tubing geometry dimensions in a digital format to operators using laser and ultrasonic technologies. The collected data is analyzed to determine the volume required for cement displacement, identify the most suitable packer fit pipes, and identify thicker pipes for mitigating casing wear.
“We recently had a Prime Mapping job with a North Sea operator that needed to identify the best packer fit pipes for 13 3/8”, 9 5/8” and 9 7/8” sections,” explains Daniel. “VFS technicians went to the operator’s yard and with the In-pipe Rover they evaluated several casings and provided a comprehensive tally list with min/max/avg ID data, drift pass/fail, pipe inner volume and maximum ovality data. This was carried out in only one day while previous suppliers could take up to 3 days with wireline trucks and logging devices. The best packer fit pipes were easily identified, facilitating the operator’s preparation before loading pipes offshore, saving up to one rig service day. Prime Mapping therefore speeds up processes and provides more accurate data”.
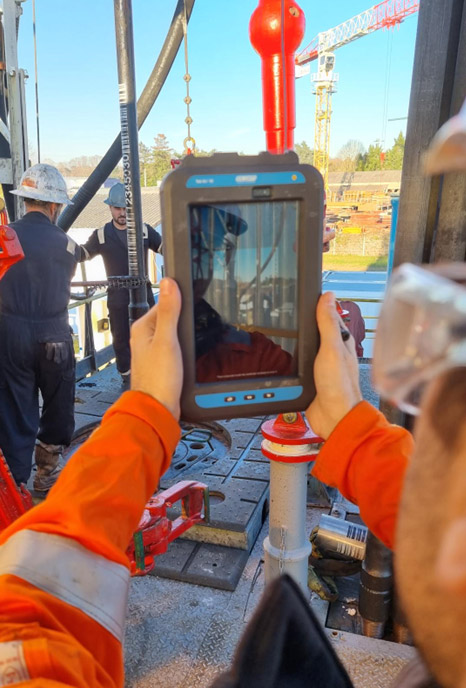
VFS has also been instrumental in the successful deployment of Vallourec’s Pre-Installed Cable Protector (PICP) which significantly improves safety by reducing the number of personnel required on the red zone and speeds up run-in-hole (RIH). In 2022, VFS technicians supervised the installation of almost 500 pipes, some of them were equipped with PICP, in a platform in the North Sea. The job was deemed a complete success with all the agreed objectives achieved. The significant gains in safety were especially highly appreciated and valued by the teams on the rig.
“More recently, VFS assisted in deploying the first long string with PICP at another platform in the North Sea”, adds Daniel. “This running was also a success, with the operator making an additional order for a third well”.
Digital solutions are also becoming increasingly prevalent in VFS’s portfolio of services offered to customers. For instance, an operator in the Caspian Sea sought digital solutions to decrease operational expenses and increase safety and productivity on the rig. VAM® Field Service, with over 15 years of experience in Azerbaijan and a long-standing collaboration with the customer in both operational management and digital transformation, proposed the implementation of Vallourec’s Running Expert solution to their operations. The digital solution was seamlessly integrated, and the customer provided positive feedback on the value the tool brought to their operations, including improved productivity and safety, time savings, and operational efficiency.
"Running Expert is a good example of our commitment to provide customers with innovation and value. Its successful deployment was made possible thanks to the strong presence of VAM® Field Service in the Caspian Sea region, our ability to seamlessly integrate digital solutions into our traditional running procedures, as well as our deep knowledge of customer running operations", says Daniel.
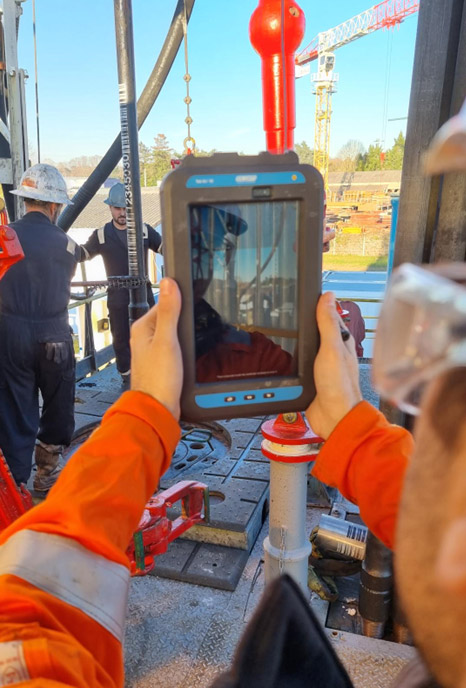
Staying close to customers – remotely
VAM® Field Services is dedicated to enhancing on-site work with a range of remote services that provide troubleshooting in critical instances. These VFS remote services, although not providing the same value as on-site services, are recommended in very specific cases such as when there are personnel-related issues, for short-term jobs, or when an urgent intervention is needed. These remote services encompass remote graph review which analyzes and evaluates critical data, enabling swift identification of potential issues and the implementation of necessary corrective measures. Additionally, remote troubleshooting empowers clients to overcome operational challenges in case of time and safety-sensitive occurrences. Through efficient communication channels and advanced technological solutions, VAM® experts can diagnose and address issues remotely, minimizing downtime and optimizing productivity.
To further elevate the convenience and accessibility of their services, VAM® recently launched the VAM® App. This user-friendly application provides direct access to the extensive knowledge and experience of VAM® experts. With the app, users can obtain real-time support, guidance, and solutions for their specific needs, all at their fingertips. This 24/7 on-demand availability ensures that assistance is readily accessible whenever it is required, regardless of time zones or geographical boundaries.
Daniel explains, “The integration of remote services by VAM® Field Services aims to fill any gaps the customers might experience during running operations by combining the convenience of remote accessibility with the expertise of VAM® professionals”. By embracing this approach, VFS strengthens its commitment to providing exceptional support and solutions to its clients, even from a distance”.
Safety and quality VFS pillars
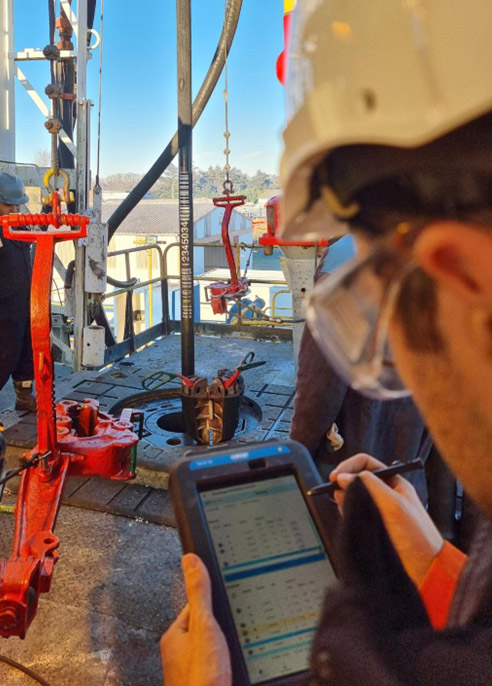
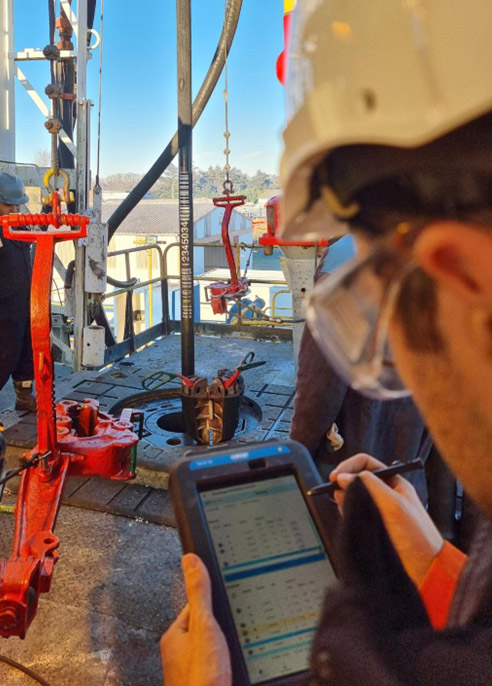
Quality is an essential pillar of VAM® Field Service, and to be the best-in-class requires a commitment to excellence that permeates in every facet of operation. One of the key components of achieving this level of quality is through the development of skills and the implementation of a comprehensive quality system ensuring that every aspect is operating at the highest possible level. Most VAM® Field Service sites are certified API Q2 which represents today the highest level of certification for quality management and above all, risk management in Oil Field Services. The API Q2 specification confirms that VAM® Field Service has robust procedures in place to ensure safety, quality, employee competency, operational efficiency, and to maintain customer satisfaction among other key quality management system elements.
Customer satisfaction is a critical component of this system, and objectives such as zero claims and detailed job reports are used to track and measure the success of these efforts. Customer scores are also an important metric used to gauge the overall effectiveness of the quality system and ensure that VFS is consistently meeting and exceeding customer expectations.
At Vallourec, safety remains our highest priority. Operating across multiple rigs, our VFS teams possess the ability to easily identify safety issues and take immediately take action. Their extensive experience and expertise in rig operations serve a vital function in enhancing safety measures and establishing benchmarks for good and undesirable safety practices.
Continuously innovating
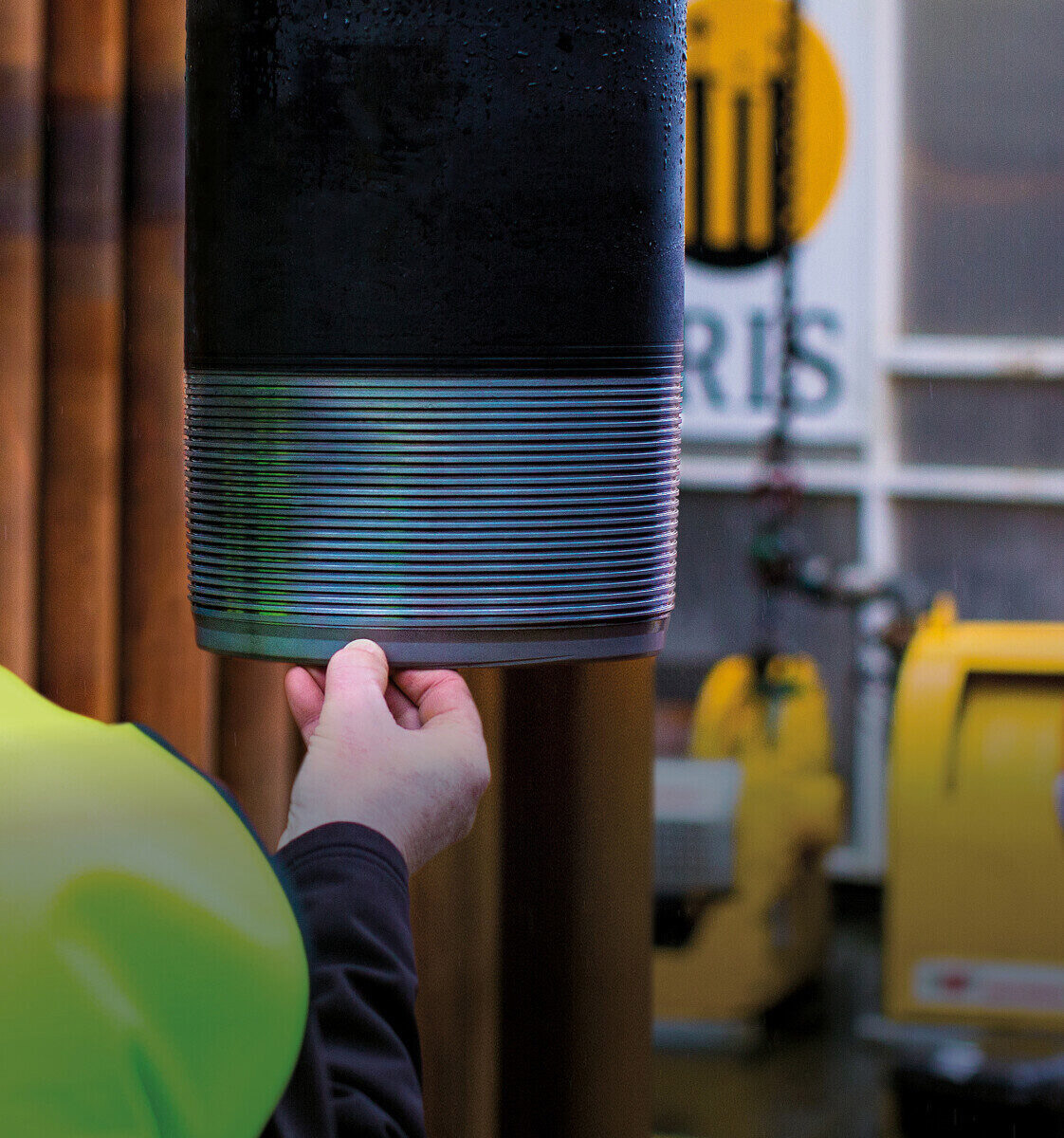
VAM® Field Service has played a pivotal role in implementing Vallourec’s new services and solutions in customers’ operations. Through a steadfast commitment to excellence, VFS continuously strives to exceed customer expectations and drive long-term success in the oil and gas industry. “VFS technicians have supported oil and gas operators for decades,” Daniel concludes, “and we intend to ensure our offer develops in line with evolving industry needs moving forward”.
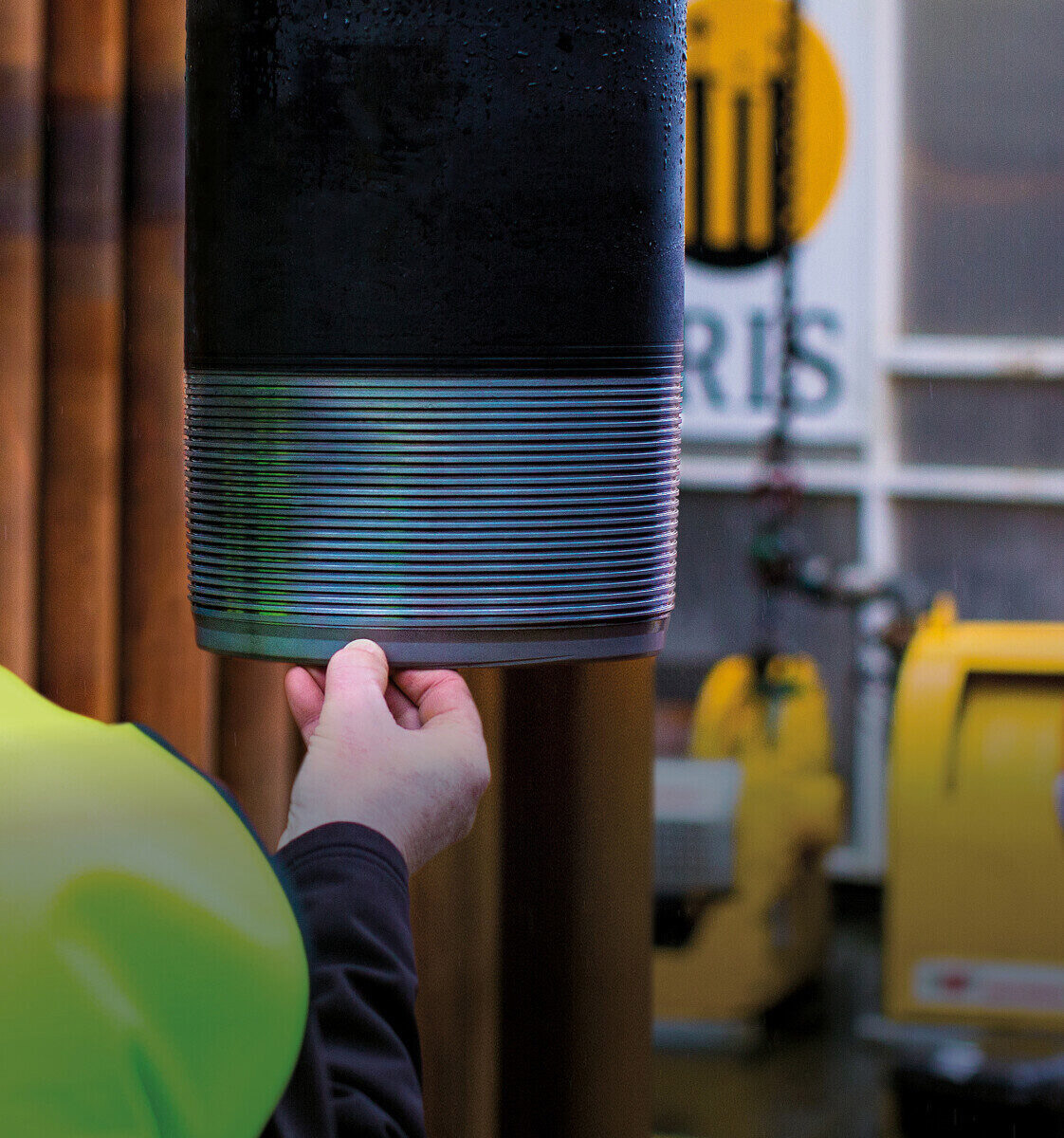