Turning remote working into an opportunity
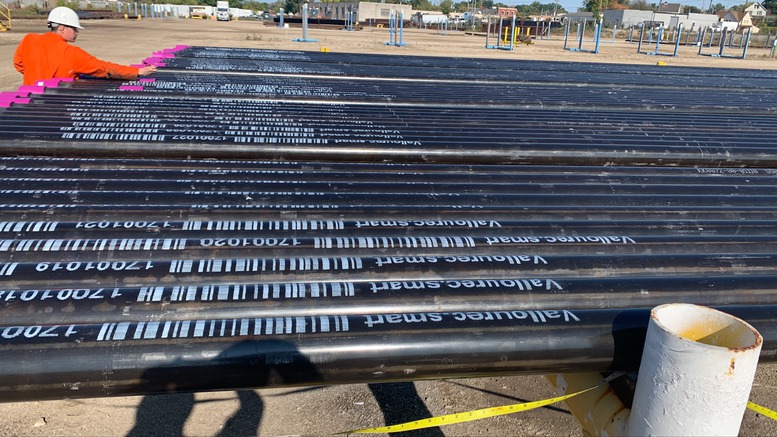
Turning remote working into an opportunity to enhance efficiency within our industry in the COVID-19 era and beyond
14/10/2020 – Digital
The COVID-19 pandemic presented Vallourec with the challenge of organizing remote working for teams while upholding its high-quality service for clients and licensees. We leveraged strong teamwork and innovative technologies to find new ways of doing business that saw us through lockdown and revealed benefits that will long outlast the pandemic.
Whether to optimize our operational performance with Industry 4.0 or as part of our business solutions portfolio with Vallourec.smart, the Group’s digital and services offering, we remain driven by our ambition to improve our competitiveness and that of our customers.
Over the last decade, the expanded use of remote technologies has led to reductions in travel costs and risks associated with onsite maintenance and inspection. Prior to the pandemic, Vallourec had proactively begun to deploy remote solutions to add value for customers and facilitate internal collaboration. Responding to the need to accelerate our progress, we have now standardized the use of technologies ranging from Microsoft Teams to RealWear and our in-house solution, Remobot.
Distancing yields unexpected benefits
Along with the rest of the world, Joe Hill had never heard of COVID-19 when he first presented his idea for using RealWear at Vallourec’s annual Winnov’ in-house innovation event in 2019. He just saw the device’s potential advantages in remote assistance situations.
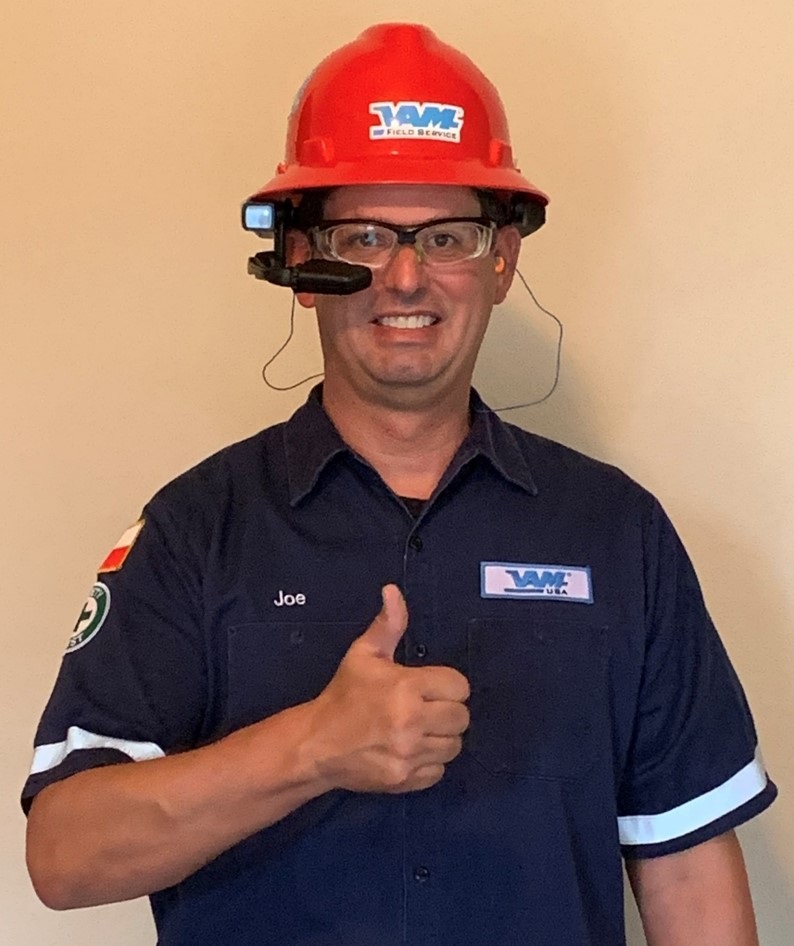
Hill bought examples of both and began working on a proof of concept. Then came COVID, and suddenly Hill’s idea was incredibly relevant, and its development urgent. Both devices were put to use.
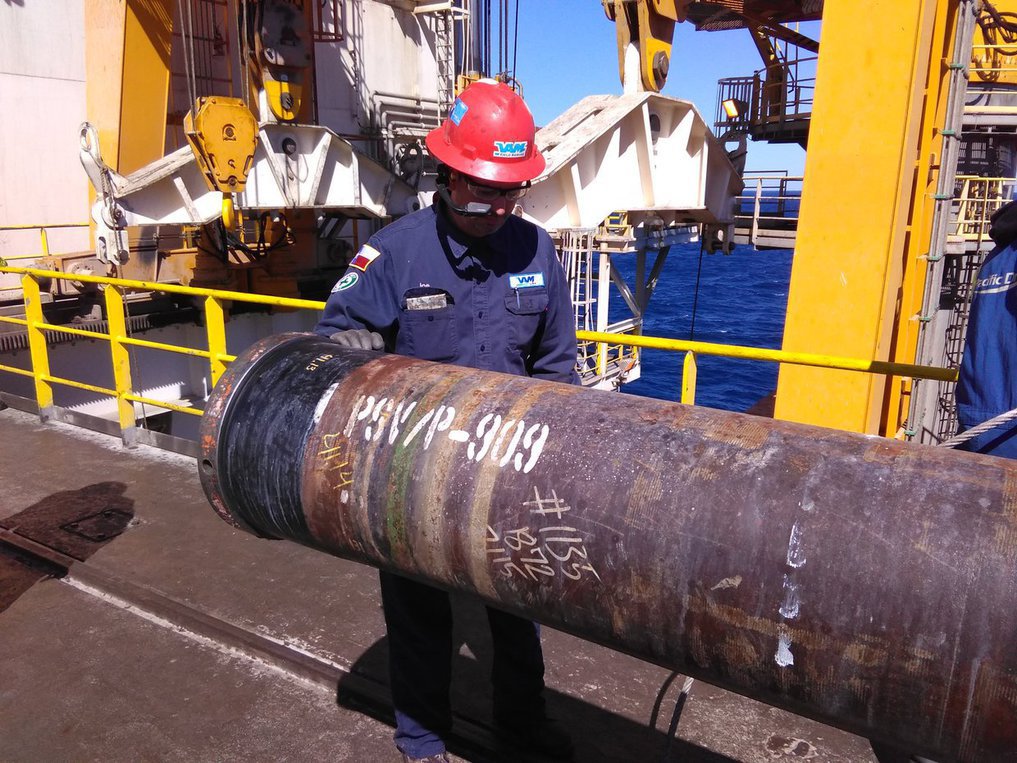
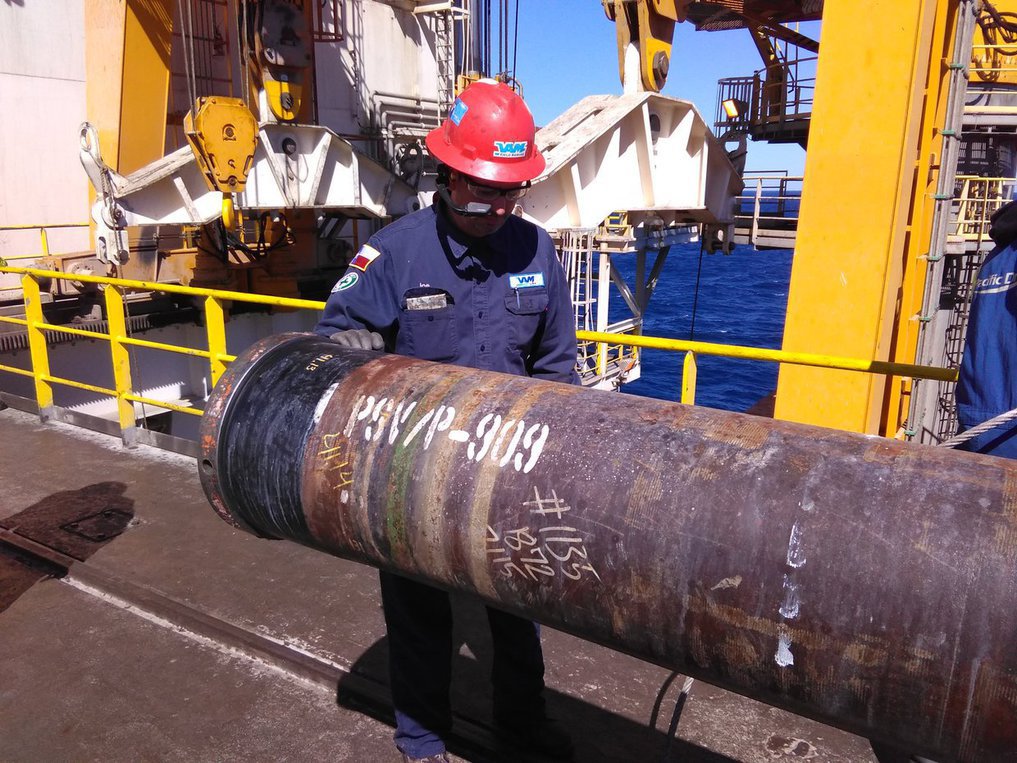
RealWear on the rig
The RealWear connected hardhat has both a visual component and a built-in mic that picks up a wearer’s audio while deadening background noise. It enables offsite personnel to follow an onsite inspector’s line of vision, giving them information, indicators and documents remotely and in real time.
“For our purposes on the rig, we ultimately chose RealWear,” Hill says. “It’s a robust, cost-effective piece of equipment. And it’s safe for use on oil rigs because it’s certified not to make a spark.”
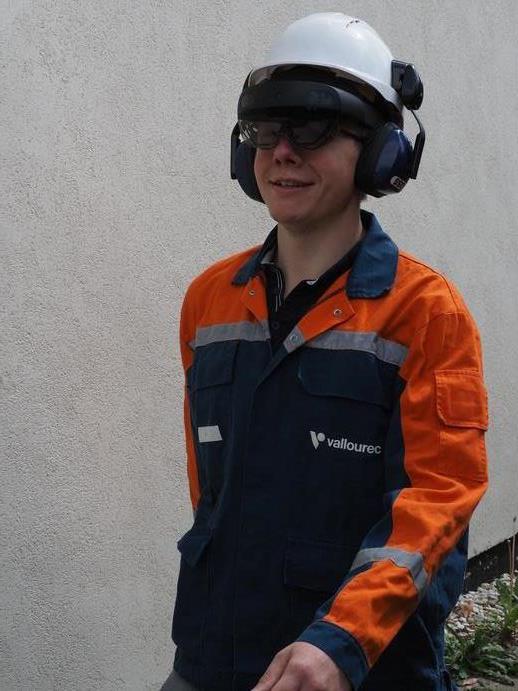
RealWear and HoloLens for remote mill inspections
For customers who want to conduct remote mill inspections, both HoloLens and RealWear are options. Damien Barbier, Thermal Expert Manager - Europe/Africa Region, has found these to be efficient solutions. Working at the Vallourec Service Center, he has already used these devices with one of our key customers. “I made a complete tour of the center, and our customer could see all relevant checkpoints right from his office,” Barbier says. “We got great customer feedback.”
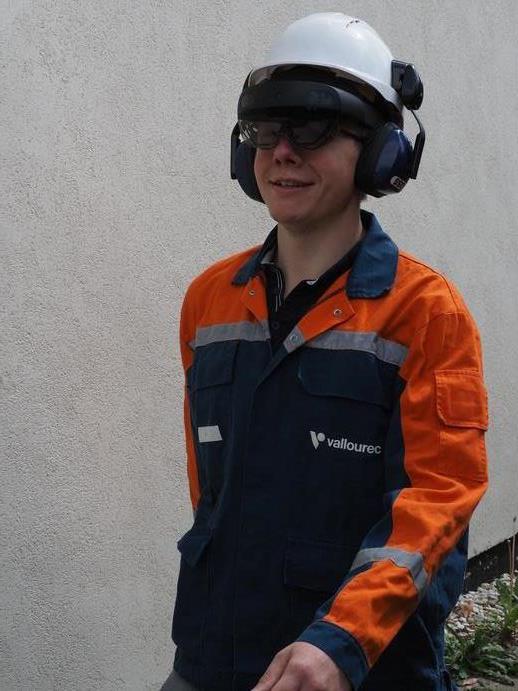
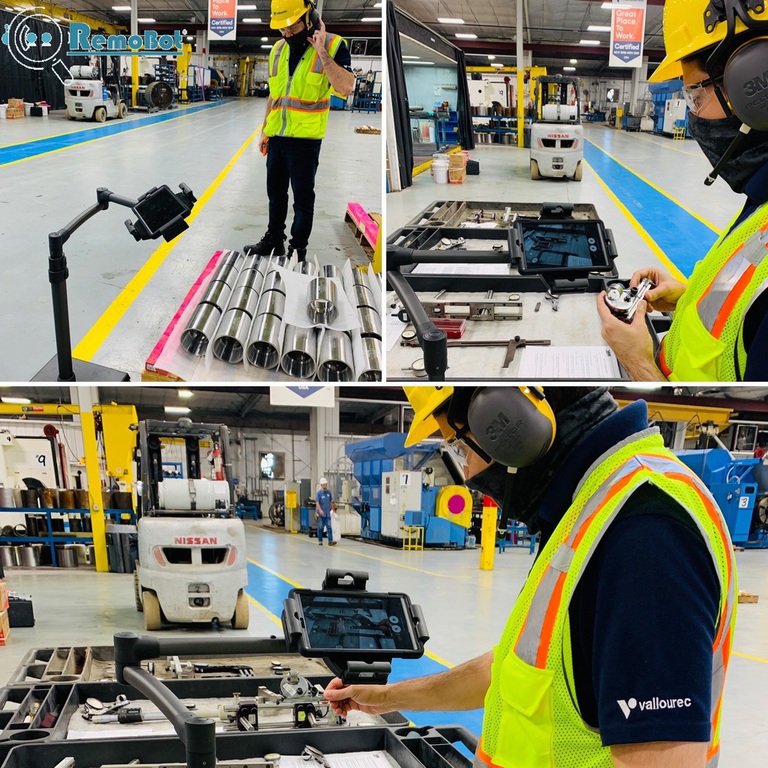
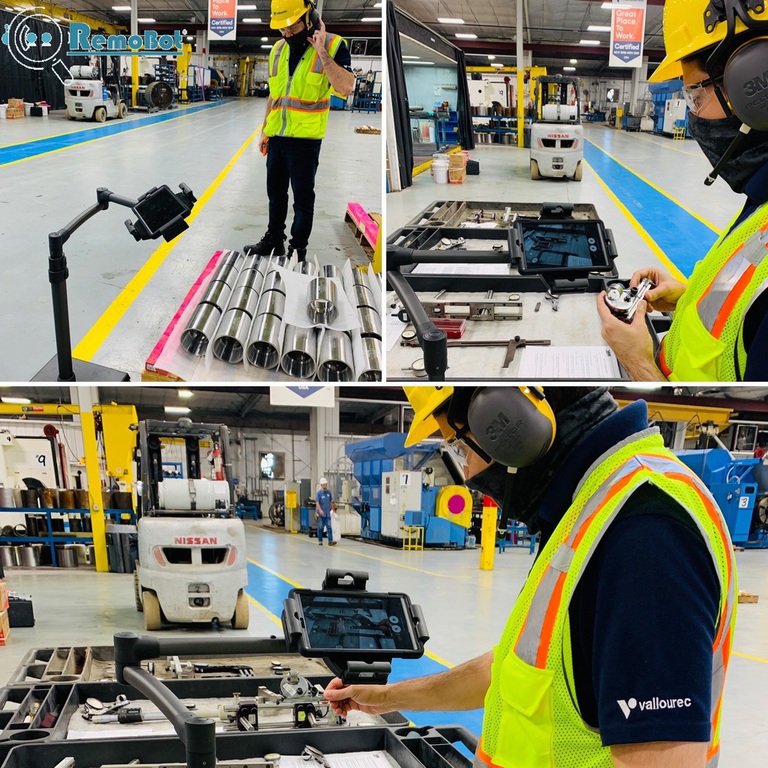
Meet Remobot, our in-house solution
Edson Viveiros, CAPEX and Continuous Improvement Manager at Vallourec Tube Alloy (USA), has taken remote assistance a step further with his new Remobot. The small robotic device combines wheel-mounted full-motion arms with a stand equipped with a connected tablet. Vallourec is using the cutting-edge robot along with RealWear to offer efficient, safe and cost-effective solutions to the challenge of conducting audits, inspections and product line reviews.
Samuel Lecerf, QHSE and Industrialization Director – Europe/Africa Region, explains the benefits of these devices from a customer standpoint: “If I’m a customer using a third-party inspector for surveillance of Vallourec, this remote technology offers amazing flexibility. In two minutes, I can connect for a virtual visit of the mill. No COVID risk, no need for me to travel to the site. It removes a lot of the logistical issues.”
Rising to the challenge of licensee support
COVID-19 brought new challenges to certify the network of VAM® connections licensees who manufacture or repair Oil Country Tubular Goods (OCTG) pipes and accessories. However, remote technology enabled us to continue monitoring and helping licensees so that we could maintain the trust VAM® users place in our network.
“We had three urgent challenges,” explains Philippe Deletombe, Quality Manager for VAM® Services, Vallourec’s support organization for licensees. “Firstly, we needed to verify and close up corrective actions from the previous year’s audits. Secondly, we needed to manage the remote qualification of licensees for new VAM® connections in our portfolio. Lastly, our licensees need TPI Licensee Technical Representative (LTR) validation. This was critical, as without the approval of an LTR inspector, licensees cannot release orders.”
To meet these needs, Vallourec connected with licensees through Microsoft Teams and RealWear while also using tools like webcams, fixed cameras and cell phones.
The team worked to streamline the process, and in the end was able to respond on time to 100% of requests for qualification received.
François David, VAM® Services General Manager, agrees that these new devices can’t fully supplant onsite presence across the board.
Great teamwork leads to benefits across the board