A Serimax success in the Nigerian waters
A Serimax success in the Nigerian waters
26/02/2020 – Welding
Congratulations to the Serimax teams for successfully completing the IDOHO project with Subsea 7 and Exxon Mobil!
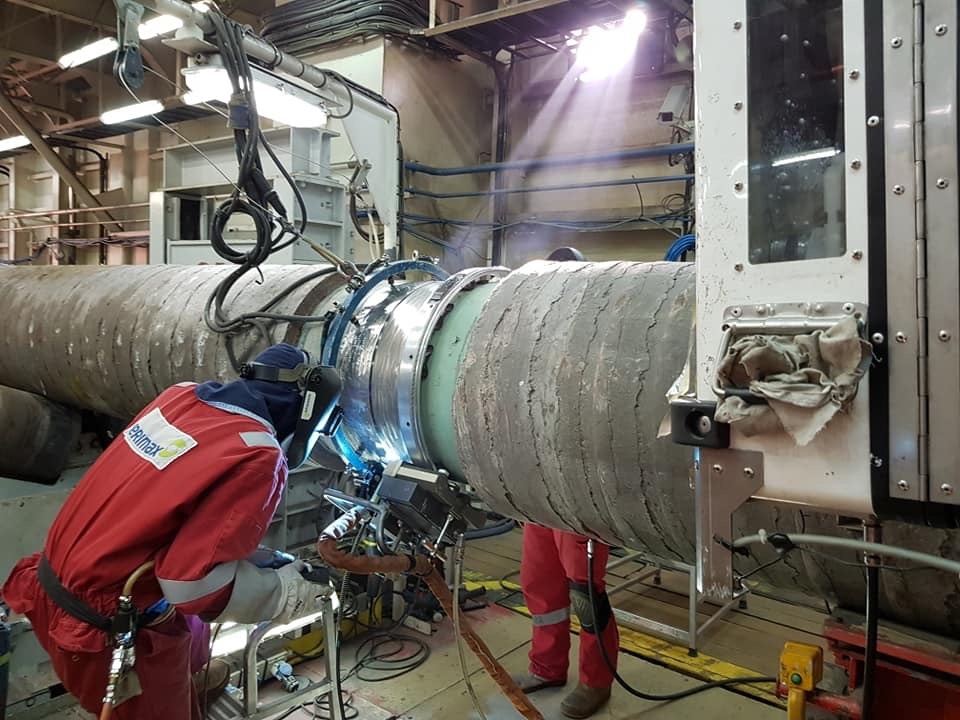
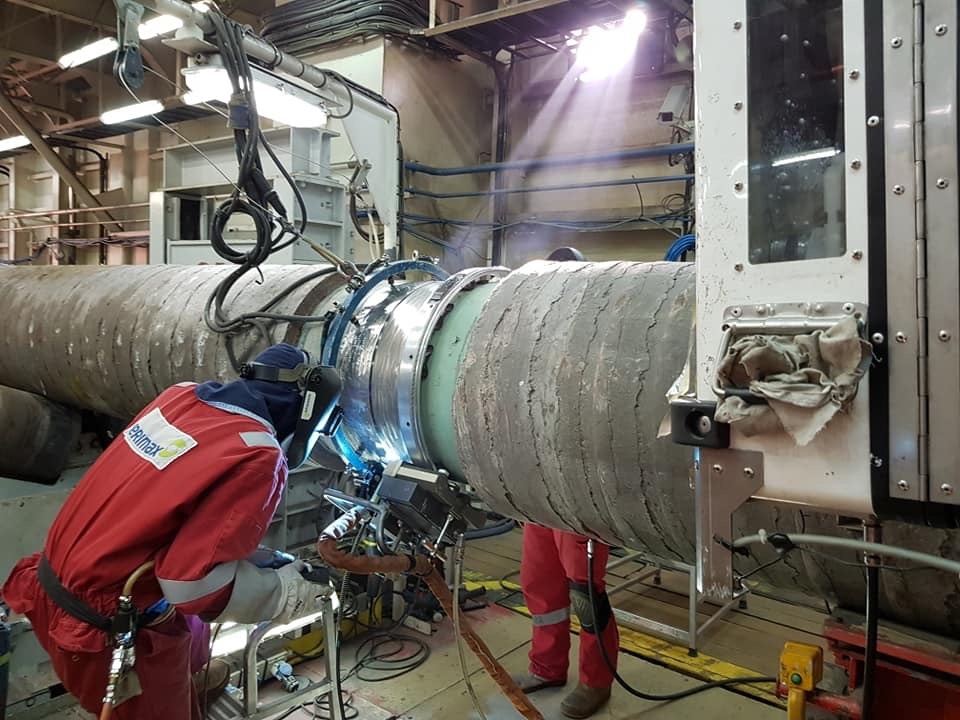
Origin of the project
The IDOHO field is located offshore Nigeria, in the bight of Bonny (Akwa Ibom State), at approximately 2 miles from shore and south of the onshore QIT (Qua Iboe Terminal) with a water depth of approximatively 57 feet.
To secure terminal supplying, Mobile Producing Nigeria, the Nigerian branch of the world’s largest publicly traded international oil and gas company Exxon Mobil, collaborated with Subsea 7, a subsea engineering, construction and services company to establish new corrosion resistant pipelines.
The pipelines implemented were corrosion resistant alloy (CRA) at first, then a carbon steel scope was added. While carbon steel pipes are made of carbon only, CRA pipes’ inside coating is made from stainless steel or a nickel-based alloy. The cost of CRA material is therefore significantly higher than carbon steel and requires specific cares from its production to final usage.
Serimax's successful involvement…
Serimax, Vallourec’s subsidiary specialized in welding, was awarded the project in March 2018 and cooperated with Subsea 7 and ExxonMobil until July 2019. The qualification of welding procedures took place at Pasir Gudang in Malaysia, since the pipes were produced in Batam. Then, aboard Subsea 7’s Antares vessel, Serimax successfully managed the provision of automatic and manual equipment, maintenance teams and main line welding teams – about 40 people from 5 different nationalities!
The project was a success for Serimax: performed with an overall repair rate of less than 2%, it once again demonstrated the strong involvement of our teams in a challenging and demanding environment. Excellence of Serimax personnel and equipment, flexibility, reactivity, understanding of client and operator needs were some of the main contribution factors.
…Not without the help of cutting-edge technologies
The IDOHO project was the opportunity to employ and showcase some of our internally developed advanced technical solutions. Cleverscan, for example, a pipe end measurement tool, is used to measure pipes’ inside and outside diameter, wall thicknesses, with the help of laser inspection. Collected data are then treated using specific software allowing determination of best way to match pipes together and gain in productivity and quality.
Scanvision is another technology utilized during the project. It is an internal visual inspection system which was on this project installed near the ILUC (internal line-up clamp, which maintains two pipes in position). The camera inspects the welding base and helps visualize the root pass from the inside for non-destructive testing, thus ensuring that it remains as per requirements.